PVDF LINED Check VALVES
Check valves play a critical role in preventing backflow, safeguarding equipment, and maintaining the integrity of processes across sectors such as mining, water treatment, chemical processing, and agriculture
Chemical Resistance
Thermal Stability
Purity
UV and Radiation Resistance
Flame Retardancy
Our Story
Understanding Check Valves and Their Components
Check valves, also known as non-return valves, allow fluid (liquid or gas) to flow in one direction while preventing reverse flow. They operate automatically, relying on the flow velocity and pressure differential to function without external actuation. This automatic operation is essential in remote or unmanned installations common in vast landscapes.
- Valve Body: Connects to the pipeline and houses internal components.
- Closure Mechanism: The moving part that permits forward flow and blocks reverse flow (e.g., swing disc, lift piston, ball).
- Seat: Provides a sealing surface to prevent backflow.
- Guides and Springs: Assist in alignment and responsiveness of the closure mechanism.
What is PVDF?
Polyvinylidene Fluoride (PVDF) is a high-performance thermoplastic fluoropolymer known for its exceptional chemical resistance, mechanical strength, and versatility. Manufactured under brand names like Kynar® PVDF, it is produced by the polymerization of vinylidene fluoride. PVDF offers a unique combination of properties that make it ideal for use in harsh industrial environments.
Key Properties of PVDF
- Chemical Resistance: Outstanding resistance to a wide range of aggressive chemicals.
- Mechanical Strength: High tensile strength and rigidity.
- Thermal Stability: Maintains performance across a broad temperature range.
- Purity: Low levels of extractables and leachables.
- UV and Radiation Resistance: Excellent stability under UV exposure and radiation.
- Flame Retardancy: Inherent resistance to ignition and flame spread.
Benefits of Using PVDF Lining in Check Valves
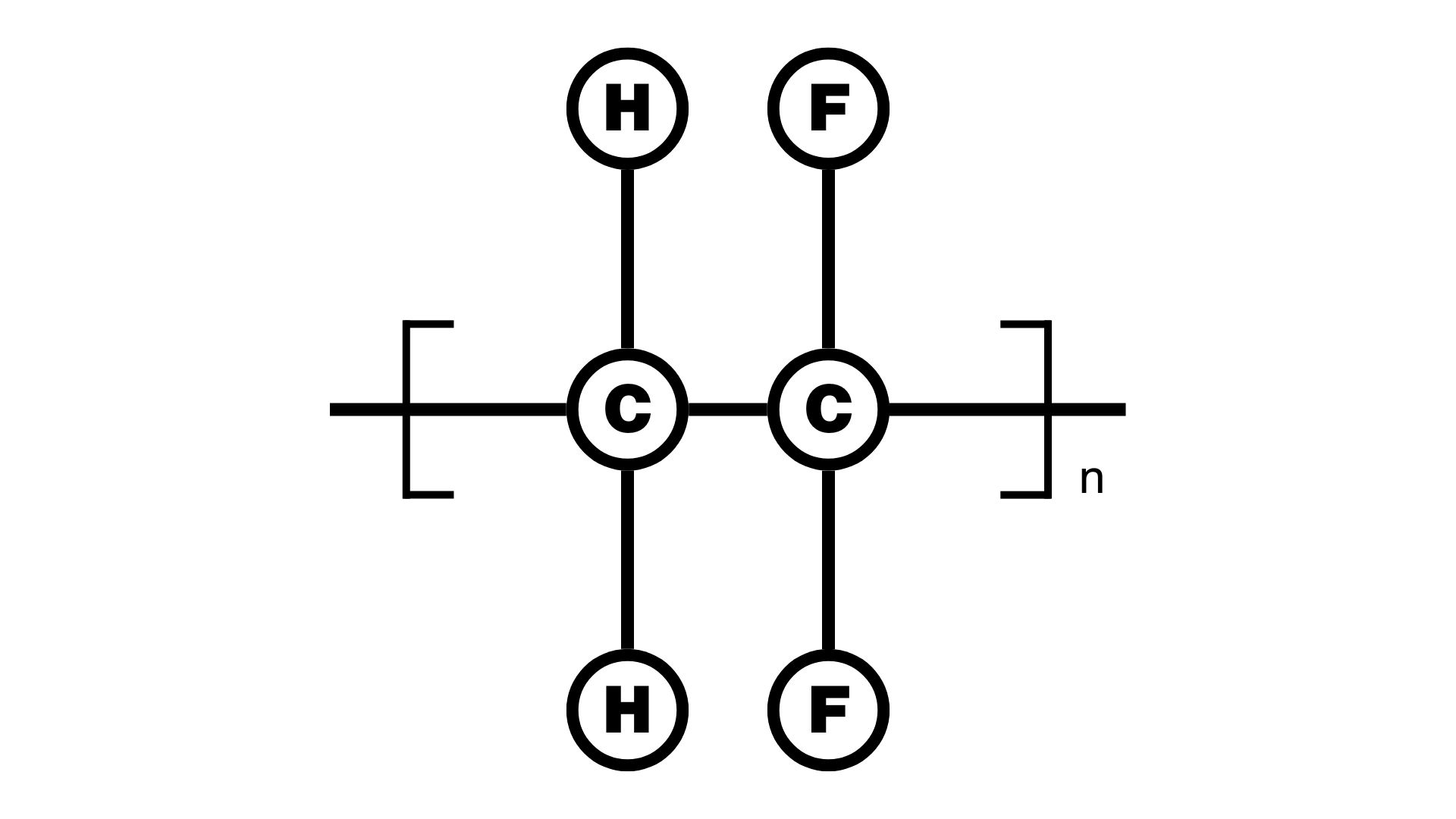
1. Exceptional Chemical Resistance
Industries often handle aggressive chemicals:
- Mining Sector: Acidic leachates and slurries in mineral extraction.
- Water Treatment: Chlorine and other disinfectants in municipal and industrial water supplies.
- Agriculture: Fertilizers and pesticides in irrigation systems.
PVDF-lined check valves resist corrosion from these substances, ensuring longevity and reducing maintenance costs.
2. Adaptability to Harsh Environmental Conditions
Environmental challenges pose unique demands:
- UV Exposure: PVDF’s UV resistance makes it suitable for outdoor installations under intense sunlight.
- Temperature Extremes: Performs reliably from scorching heat to cooler climates.
- Remote Locations: Durable valves reduce the need for frequent servicing in hard-to-reach areas.
3. Prevention of Contamination in Sensitive Applications
- Food and Beverage Industry: PVDF prevents contamination in processes adhering to strict food safety standards.
- Pharmaceuticals: Maintains purity in drug manufacturing, aligning with regulatory requirements.
- Semiconductor Manufacturing: Supports high-purity requirements in technological industries.
4. Compliance with Industry Standards
PVDF-lined check valves can meet or exceed local regulations:
- Potable Water Standards: Suitability of products in contact with drinking water.
- Flange Standards: Compliance with flange dimensions and pressure ratings.
- Certification Marks: Ensures products comply with relevant codes.
5. Mechanical Reliability
- Mining and Resources: Withstands abrasive slurries and high-pressure systems prevalent in mining operations.
- Oil and Gas: Durable against corrosive substances extracted in offshore and onshore facilities.
6. Fire Safety Enhancements
Given susceptibility to fires:
- Flame Retardancy: PVDF’s low flammability adds a layer of safety.
Low Smoke Emission: Reduces risk in enclosed facilities.
Applications of PVDF-Lined Check Valves
Mining and Mineral Processing
- Acidic and Abrasive Slurries: Managing the harsh conditions of mineral extraction.
- Tailings Management: Preventing backflow in tailings pipelines to protect the environment.
Water and Wastewater Treatment
- Desalination Plants: Essential in areas where seawater is treated for potable use.
- Remote Community Water Supplies: Durable valves reduce maintenance in isolated regions.
Agriculture and Irrigation
- Fertilizer Injection Systems: Preventing contamination of water sources.
- Pumping Stations: Ensuring reliable operation in extensive irrigation networks.
Chemical Processing
- Industrial Chemicals: Handling caustic and acidic substances used in manufacturing.
- Safety Systems: Protecting personnel and equipment from hazardous backflow.
Oil and Gas Industry
- Corrosive Fluids: Managing substances extracted during drilling and production.
- Pipeline Protection: Preventing reverse flow that could lead to spills or equipment damage.
Infrastructure Projects
- Stormwater Management: Preventing backflow in drainage systems during heavy rains.
Firefighting Systems: Reliable components in systems critical for emergency response.
Selecting the Right PVDF-Lined Check Valve
- Compliance: Ensure the valve meets relevant standards and certifications.
- Environmental Conditions: Select valves designed to withstand local climate challenges.
- Chemical Compatibility: Match PVDF’s resistance to the specific chemicals in use.
- Installation Requirements: Consider accessibility for maintenance in remote areas.
Supplier Support: Choose suppliers familiar with regulations and offering local support.
Maintenance of PVDF-Lined Diaphragm Valves
Installation
- Follow Local Codes: Adhere to plumbing and installation standards.
- Proper Orientation: Install valves correctly to handle the specific flow rates and pressures.
- Protection Against Elements: While PVDF is UV resistant, additional shielding can prolong valve life in extreme conditions.
Maintenance
- Regular Inspections: Schedule maintenance according to the operational demands and environmental exposure.
- Spare Parts Availability: Ensure availability of parts locally to minimize downtime.
- Training: Provide training for maintenance personnel on the specifics of PVDF-lined valves.
PVDF-lined check valves offer industries a robust solution for enhancing system reliability and efficiency. Their exceptional chemical resistance, adaptability to harsh environmental conditions, and compliance with standards make them an invaluable asset across various sectors. By investing in PVDF-lined check valves, businesses can ensure long-term operational success, safety, and adherence to regulatory requirements.