PVDF LINED Ball Valves
These valves with Polyvinylidene Fluoride (PVDF) lining gain enhanced properties that make them exceptionally suitable for handling corrosive, high-purity, and high-temperature applications.
Smooth Internal Surfaces
Ease of Operation
Versatile Connection Options
Automation Compatibility
Operational Simplicity
Our Story
Understanding Ball Valves and PVDF Material
Ball valves are quarter-turn valves that utilize a hollow, perforated, and pivoting ball to control fluid flow. When the ball’s hole aligns with the flow, the valve is open; when rotated 90 degrees by the valve handle or actuator, the flow is blocked. Key components include:
-
- Valve Body: The outer shell that houses the internal parts and connects to the piping system.
- Ball: The spherical closure unit that regulates flow.
- Stem: Connects the ball to the actuator or handle.
- Seats and Seals: Provide tight sealing to prevent leakage.
- Actuator or Handle: Facilitates manual or automated operation.
What is (PVDF)
PVDF is a high-performance thermoplastic fluoropolymer known for its remarkable chemical resistance, mechanical strength, and thermal stability. Its properties make it an ideal material for manufacturing ball valves intended for aggressive and high-purity applications.
Key Properties of PVDF
- Chemical Inertness: Resistant to a wide array of chemicals, including acids, bases, and organic solvents.
- High Purity: Low levels of extractables and leachables, critical for contamination-sensitive processes.
- Thermal Stability: Operational integrity maintained over a broad temperature range (-40°C to +150°C).
- Mechanical Strength: Excellent resistance to wear, abrasion, and impact.
- UV and Radiation Resistance: Suitable for outdoor and radiation-exposed environments.
Advantages of PVDF Ball Valves
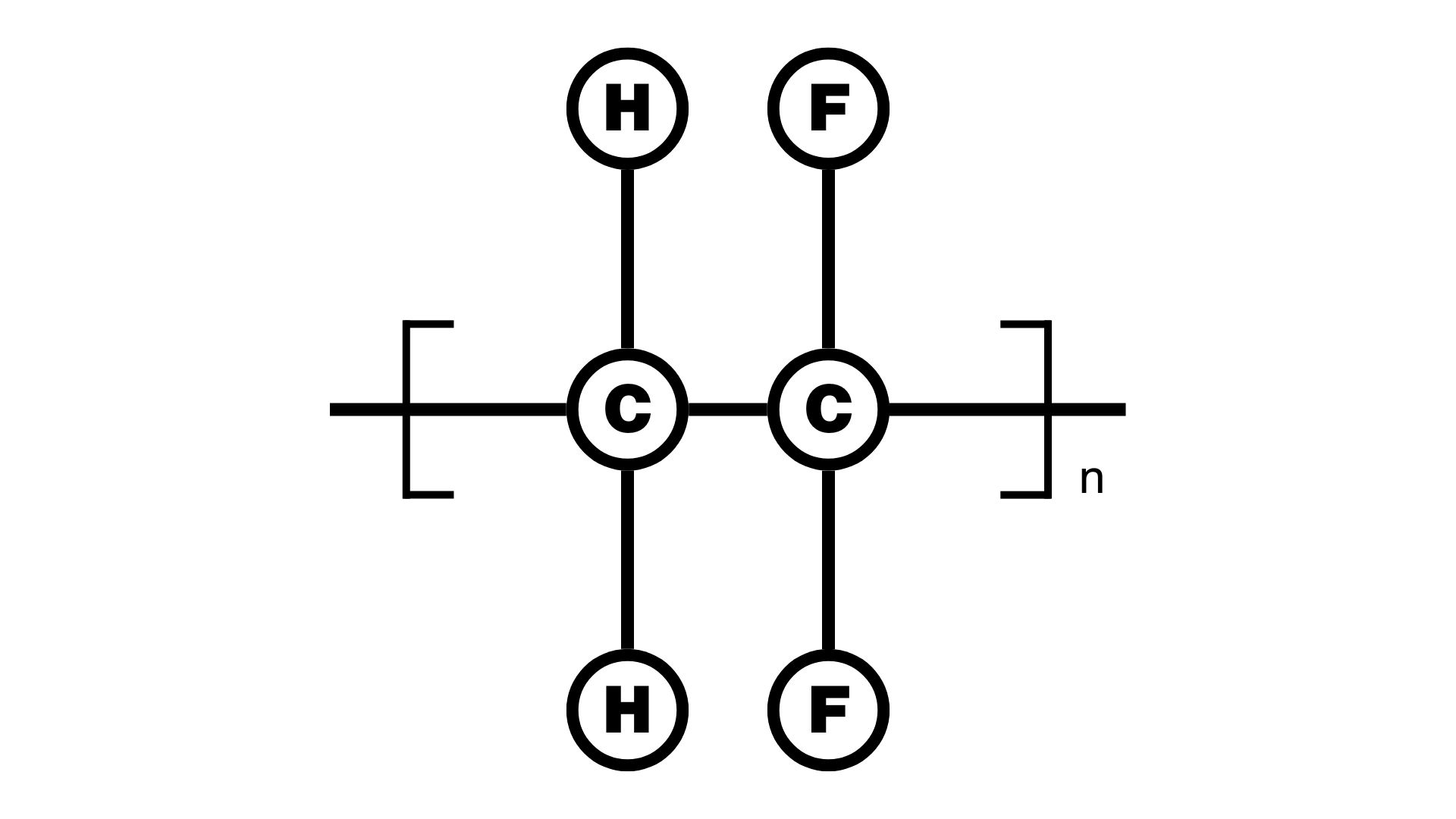
Exceptional Chemical Resistance
PVDF ball valves offer superior resistance to corrosive chemicals, making them suitable for:
- Aggressive Acids: Sulfuric acid, hydrochloric acid, nitric acid.
- Strong Alkalis: Sodium hydroxide, potassium hydroxide.
- Organic Solvents: Alcohols, esters, ketones.
- Oxidizing Agents: Chlorine, bromine.
This broad chemical compatibility ensures longevity and reliability in harsh chemical environments, reducing maintenance costs and downtime.
High Purity and Contamination Prevention
In industries where purity is paramount, PVDF’s low extractable levels prevent contamination of the process media. Applications include:
- Pharmaceuticals: Maintaining sterility in drug manufacturing.
- Semiconductors: Handling ultra-pure water and chemicals without introducing impurities.
- Food and Beverage: Ensuring hygienic conditions in processing and packaging.
Thermal Performance
PVDF ball valves maintain performance across wide temperature ranges:
- Cryogenic Temperatures: Remain operational at low temperatures without becoming brittle.
- High Temperatures: Withstand elevated temperatures up to +150°C without deformation or loss of mechanical properties.
This makes them versatile for processes involving temperature extremes.
Mechanical Durability
PVDF’s robust mechanical properties provide:
- Wear Resistance: Prolonged life even in abrasive applications.
- Impact Resistance: Withstands mechanical shocks and vibrations.
- Pressure Handling: Suitable for high-pressure applications due to structural integrity.
UV and Weather Resistance
PVDF ball valves can be used in outdoor applications where exposure to sunlight and weather conditions is a factor. They resist degradation from UV radiation, ensuring sustained performance over time.
Fire Safety
PVDF is inherently flame-retardant:
- Low Flammability: High limiting oxygen index (LOI) reduces fire risk.
- Minimal Smoke and Toxicity: Generates less smoke and fewer toxic gases if exposed to fire.
Lightweight Construction
Compared to metal valves, PVDF ball valves are lighter, facilitating easier installation and reducing support requirements in piping systems.
Applications of PVDF Ball Valves
Chemical Processing
- Corrosive Fluid Handling: Safe transfer of aggressive chemicals without risk of valve degradation.
- Batch Processing: Precise control over chemical dosing and mixing.
Water and Wastewater Treatment
- Disinfection Systems: Handling chlorine and other disinfectants.
- pH Control: Managing acids and bases in neutralization processes.
Pharmaceutical and Biotechnology
- Sterile Processes: Maintaining aseptic conditions in production.
- Clean Utilities: Distribution of purified water and clean steam.
Food and Beverage Industry
- Ingredient Handling: Safe transport of liquids without contamination.
- Cleaning Processes: Resistant to cleaning agents used in sanitation protocols.
Semiconductor Manufacturing
- Ultra-Pure Water Systems: Preventing contamination in critical rinse processes.
- Chemical Delivery: Handling high-purity chemicals used in wafer fabrication.
Mining and Mineral Processing
- Leaching Operations: Managing corrosive leachates in metal extraction.
- Slurry Handling: Durable against abrasive slurries containing particulate matter.
Power Generation
- Chemical Feed Systems: Controlling additives in boiler feedwater.
- Flue Gas Treatment: Handling reagents in emission control systems.
Selecting the Right PVDF Ball Valve
When choosing a PVDF ball valve, consider:
- Chemical Compatibility: Verify PVDF’s resistance to the specific chemicals in use.
- Temperature and Pressure Ratings: Ensure the valve meets operational requirements.
- Valve Size and Port Configuration: Select appropriate sizes and consider full-port designs for minimal flow restriction.
- Connection Type: Choose between threaded, flanged, or welded ends based on the piping system.
- Actuation Needs: Decide on manual or automated operation depending on process control requirements.
- Standards and Certifications: Look for compliance with industry standards like FDA, USP Class VI, or NSF/ANSI as applicable.
Installation and Maintenance Guidelines
Tips
- Alignment: Ensure proper alignment to prevent stress on the valve body and connections.
- Support: Provide adequate support to prevent excessive load on the valve.
- Torque: Follow manufacturer specifications for tightening to avoid damaging seals or threads.
Maintenance Practices
- Regular Inspection: Check for signs of wear, leaks, or damage.
- Cleaning: Use compatible cleaning agents to avoid degrading PVDF components.
- Spare Parts: Keep essential spare parts like seats and seals available for quick replacements.
- Actuator Maintenance: If automated, maintain actuators per manufacturer recommendations to ensure reliable operation.
Advantages Over Other Valve Types
Compared to diaphragm and butterfly valves, PVDF ball valves offer:
- Tight Shut-Off: Provides bubble-tight sealing, essential for preventing leaks of hazardous substances.
- Full Bore Design: Allows unobstructed flow, minimizing pressure drop and facilitating pigging operations in pipelines.
- Operational Simplicity: Easy to operate and maintain, with fewer moving parts.
Frequently Asked Questions
- What specific chemicals can PVDF ball valves safely handle?
PVDF is compatible with a broad range of chemicals, making it ideal for aggressive substances that would typically damage other materials. - How do PVDF ball valves compare to PTFE and other fluoropolymers?
PVDF is more mechanically robust than some fluoropolymers, like PTFE, providing enhanced durability in systems requiring both chemical resistance and physical strength. - Which industries benefit most from using PVDF ball valves?
PVDF ball valves are especially useful in industries that prioritize chemical resistance, durability, and purity control, such as pharmaceuticals, chemical processing, water treatment, and electronics. - What are the environmental impacts of using PVDF materials in industrial applications?
PVDF valves are durable and reduce maintenance needs, potentially minimizing waste over time. However, the production and disposal processes have certain environmental considerations.
PVDF ball valves represent a significant advancement in valve technology for industries dealing with corrosive, high-purity, and high-temperature applications. Their unique combination of chemical resistance, mechanical strength, thermal stability, and purity makes them an excellent choice for enhancing process reliability and efficiency. By selecting PVDF ball valves, industries can achieve longer service life, reduced maintenance costs, and improved safety, contributing to overall operational excellence.