PVDF LINED DIAPHRAGM VALVES
These valves with Polyvinylidene Fluoride (PVDF) lining significantly improves their performance, durability, and application range.
Chemical Resistance
Thermal Stability
Purity
UV and Radiation Resistance
Flame Retardancy
Our Story
Understanding Diaphragm Valves and Their Components
Before exploring the advantages of PVDF linings, it’s essential to understand the primary components of a diaphragm valve:
- Valve Body: The main housing that contains the flow passage. It is designed to withstand internal pressures and resist external environmental factors.
- Diaphragm: A flexible membrane that acts as the closure mechanism, controlling the flow by pressing against the valve seat. Diaphragms are typically made from elastomeric materials such as rubber, PTFE, or other thermoplastics.
- Bonnet Assembly: Includes the bonnet, compressor, and support structures that secure the diaphragm and connect it to the actuator or handwheel.
- Stem: A shaft that transmits motion from the actuator or handwheel to the diaphragm, facilitating the opening or closing of the valve.
- Actuator/Handwheel: The operational mechanism used to control the valve, which can be manual (handwheel) or automated (pneumatic, electric, or hydraulic actuators).
- Lining: A protective layer applied to the internal surfaces of the valve body and sometimes the bonnet, enhancing resistance to corrosion, abrasion, and chemical attack.
What is PVDF?
Polyvinylidene Fluoride (PVDF) is a high-performance thermoplastic fluoropolymer known for its exceptional chemical resistance, mechanical strength, and versatility. Manufactured under brand names like Kynar® PVDF, it is produced by the polymerization of vinylidene fluoride. PVDF offers a unique combination of properties that make it ideal for use in harsh industrial environments.
Key Properties of PVDF
- Chemical Resistance: Outstanding resistance to a wide range of aggressive chemicals.
- Mechanical Strength: High tensile strength and rigidity.
- Thermal Stability: Maintains performance across a broad temperature range.
- Purity: Low levels of extractables and leachables.
- UV and Radiation Resistance: Excellent stability under UV exposure and radiation.
- Flame Retardancy: Inherent resistance to ignition and flame spread.
Years Of Experience
Renovation Projects
Custom Build Pieces
Installations
Benefits of Using PVDF Lining in Diaphragm Valves
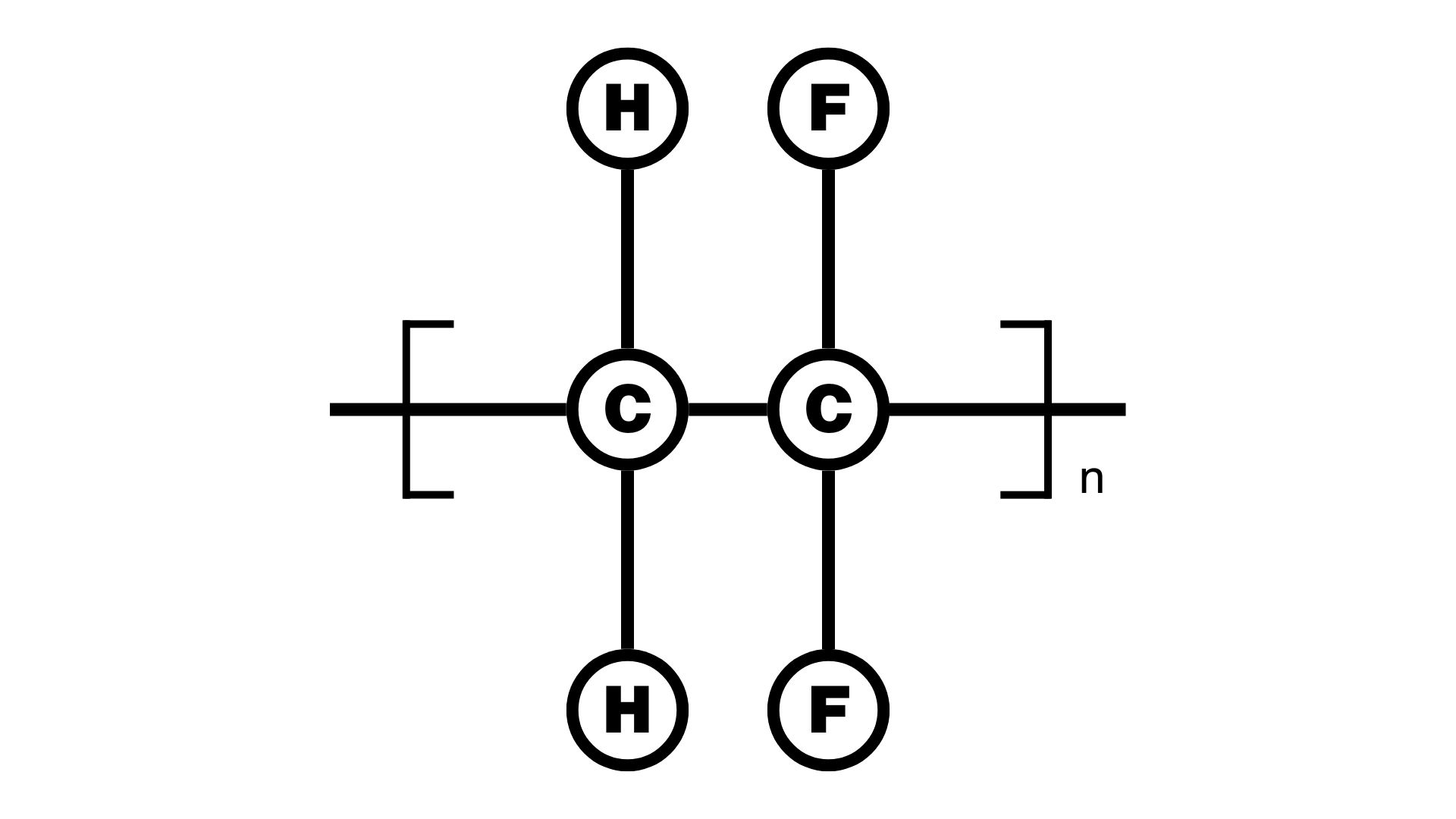
Incorporating PVDF as a lining material in diaphragm valves offers numerous advantages:
1. Superior Chemical Resistance
PVDF exhibits exceptional resistance to a vast array of chemicals, including:
- Acids: Resistant to strong acids like hydrochloric acid, sulfuric acid, and nitric acid.
- Bases: Withstands exposure to strong alkalis such as sodium hydroxide.
- Organic Solvents: Compatible with alcohols, aldehydes, and chlorinated solvents.
- Oxidizing Agents: Stable in the presence of oxidizers like chlorine and bromine.
This extensive chemical compatibility ensures that PVDF-lined diaphragm valves can handle aggressive and corrosive fluids without degrading, thus extending the valve’s service life and reliability.
2. High Mechanical Strength and Durability
PVDF offers excellent mechanical properties:
- High Tensile Strength: Ensures structural integrity under high pressure and mechanical stress.
- Abrasion Resistance: Withstands wear from particulate-laden fluids, suitable for slurry applications.
- Impact Resistance: Resistant to mechanical shocks and vibrations.
These attributes make PVDF-lined valves robust and long-lasting, reducing the need for frequent maintenance or replacement.
3. Broad Temperature Range
PVDF maintains its performance across a wide temperature spectrum:
- Operating Temperatures: From -40°C to +150°C (-40°F to +302°F).
- Thermal Stability: Retains mechanical and chemical resistance at elevated temperatures.
This broad range allows PVDF-lined diaphragm valves to be used in processes involving both cryogenic and high-temperature fluids, enhancing their versatility.
4. UV and Radiation Resistance
PVDF is inherently resistant to ultraviolet (UV) radiation and nuclear radiation:
- UV Stability: Does not degrade when exposed to sunlight, suitable for outdoor installations.
- Radiation Resistance: Withstands exposure to gamma and X-rays, beneficial in nuclear facilities and medical applications.
This resistance ensures long-term performance in environments where other materials might deteriorate.
5. Low Permeability and High Purity
PVDF’s molecular structure results in low permeability:
- Barrier Properties: Prevents the permeation of gases and liquids, ensuring containment of hazardous or volatile substances.
- Purity: The material does not leach contaminants, making it ideal for ultra-pure applications.
These characteristics are crucial in industries like pharmaceuticals, semiconductors, and food processing, where purity and containment are paramount.
6. Smooth Surface Finish and Non-Adherence
The smooth interior surface of PVDF linings offers multiple benefits:
- Reduced Friction: Promotes efficient fluid flow with minimal pressure loss.
- Non-Stick Properties: Inhibits the buildup of deposits and scaling, reducing maintenance requirements.
- Easy Cleaning: Facilitates cleaning and sterilization, essential for sanitary applications.
This results in improved operational efficiency and lower operational costs.
7. Fire Resistance
PVDF exhibits inherent flame retardancy:
- High Limiting Oxygen Index (LOI): Requires a high concentration of oxygen to sustain combustion.
- Low Smoke Generation: Produces minimal smoke and toxic gases when exposed to fire.
This property enhances safety in environments where fire hazards are a concern.
8. Compliance with Regulatory Standards
PVDF materials often meet stringent industry regulations:
- FDA Approval: Recognized as safe for contact with food and pharmaceuticals.
- USP Class VI Certification: Suitable for medical devices and drug processing equipment.
- NSF/ANSI 61 Certification: Approved for use in potable water systems.
- ASTM and ISO Standards: Meets international standards for material performance.
Compliance ensures that PVDF-lined diaphragm valves can be used confidently in regulated industries without legal or safety concerns.
9. Electrical Insulation Properties
PVDF is an excellent electrical insulator:
- High Dielectric Strength: Prevents electrical conductivity through the valve, enhancing safety.
- Low Dielectric Constant: Useful in applications requiring minimal electrical interference.
This makes PVDF-lined valves suitable for applications involving electrical equipment or sensitive instrumentation.
10. Cost-Effective Solution
While PVDF offers high-end performance, it remains a cost-effective option:
- Material Costs: Less expensive than exotic metals like Hastelloy or titanium.
- Longevity: Extended service life reduces the total cost of ownership.
- Maintenance Savings: Lower maintenance requirements translate to operational savings.
The balance of performance and cost makes PVDF an economically attractive choice for many industries.
Applications of PVDF-Lined Diaphragm Valves
Thanks to its unique properties, PVDF-lined diaphragm valves are suited for a wide range of applications:
-
- Chemical Processing: Handling aggressive chemicals in production and waste streams.
- Water and Wastewater Treatment: Managing chlorinated water, fluoride dosing, and other chemical treatments.
- Pharmaceutical Manufacturing: Ensuring sterile conditions in drug production and transfer.
- Food and Beverage Industry: Processing fluids where hygiene and non-contamination are critical.
- Semiconductor Fabrication: Transporting ultra-pure water and chemicals without introducing contaminants.
- Mining and Metallurgy: Controlling slurry flows and corrosive leachates.
- Pulp and Paper Industry: Managing bleaching agents and other corrosive chemicals.
- Oil and Gas: Handling sour gas and corrosive fluids in upstream and downstream processes.
- Nuclear Facilities: Withstanding radiation exposure in cooling systems and waste management.
Selecting the Right PVDF-Lined Diaphragm Valve
When choosing a PVDF-lined diaphragm valve, consider the following factors:
- Chemical Compatibility: Verify that PVDF is compatible with all chemicals in the process stream.
- Temperature and Pressure Ratings: Ensure the valve can withstand the operating conditions.
- Valve Size and Configuration: Select the appropriate size and type (e.g., weir or straight-through design) for your application.
- Actuation Method: Decide between manual operation or automation based on process control requirements.
- Standards and Certifications: Confirm that the valve meets all necessary industry and regulatory standards.
Consulting with valve manufacturers or suppliers can aid in selecting the optimal valve for your specific needs.
Maintenance of PVDF-Lined Diaphragm Valves
To maximize the lifespan and performance of PVDF-lined valves:
- Regular Inspections: Check for signs of wear, damage, or chemical attack.
- Proper Installation: Follow manufacturer guidelines to prevent undue stress or misalignment.
- Avoid Over-Pressurization: Stay within the valve’s rated pressure limits to prevent damage.
- Compatible Cleaning Agents: Use cleaning chemicals that are safe for PVDF to avoid degradation.
- Storage Conditions: Store spare valves and diaphragms in a cool, dry place away from direct sunlight.